Re|focus Sustainability Innovation Awards
Congratulations to the 2021 Re|focus Sustainability Innovation Award Winners
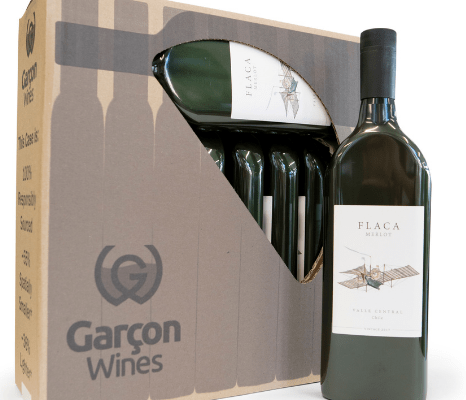
Garçon Wines is the winner of the Design category for addressing the large carbon footprint of round, glass wine bottles with a beautifully designed, space-, weight- and energy-saving flat bottle made entirely from recycled PET plastic.
Packamama's eco, flat wine bottles are an innovation that is respectful of the wine industry's heritage and a packaging industry benchmark of shape innovation, best-in-class material and recyclability by design. The design is respectfully inspired by the round, glass wine bottle but is uniquely flat to save space and made entirely from recycled PET, pre-existing not single-use plastic, to save weight and energy. The product became known for enabling delivery of a full-sized bottle of wine through an average letterbox in the UK. Today their sustainable flat bottles are being positioned as a serious challenger to round, glass wine bottles.
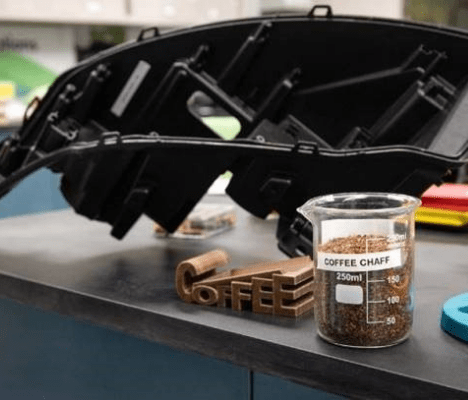
Ford Motor Company is the recipient of this year’s Materials award for a composite incorporating biocarbon from coffee manufacturing. The composite is 17% lighter, requiring 25% less energy to produce and more sustainable than the talc-filled material that was its predecessor.
This new composite material is polypropylene mixed with biocarbon fillers from coffee chaff. The coffee chaff is a waste byproduct of McDonald's coffee manufacturing process. By replacing talc with coffee chaff, both the material weight and cost are reduced while improving the material's thermal stability. With this innovative material, a waste stream is diverted from landfills, and a superior composite is produced at a 5% cost savings. Additionally, the headlamp housing unit that is the first implementation of this composite material requires 25% less energy to manufacture than existing headlamp housing material does.
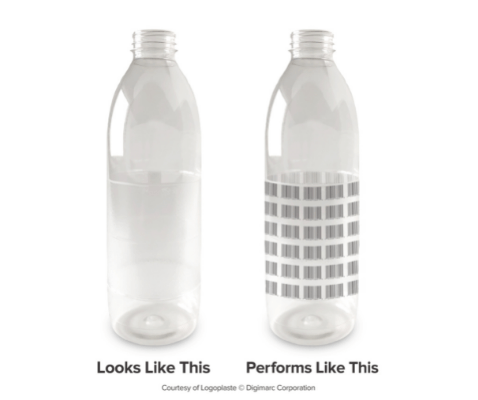
Digimarc Corporation takes home the End-of-Life award for its digital watermarking solution, giving plastics and other waste a “digital recycling passport" to increase the accuracy and efficiency of the recycling process and drive a more circular economy.
Digimarc digital watermarking technology creates a "digital recycling passport" into any printed material or plastic object. Although the digital identifier is visually imperceptible to humans, it can be detected by computing devices with cameras (smartphones, sorting machines, point-of-sale, etc.) In essence, most any media or 3D object can be turned into an ‘internet of things’ (IoT) object, linked to virtually unlimited data about the object. This enables sorting equipment and recycling facility operators to sort and filter based on the object at its unique product level, such as manufacturer, product SKU, resin type, various components of multi-layer packaging, prior food vs non-food contact, CO2 footprint, carbon-black, etc. Consumer can scan similarly enhanced packaged to obtain disposal instructions on a specific package, based on their geo-location or municipal recycler.
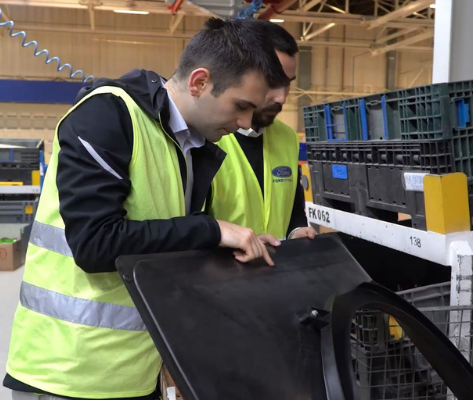
The People’s Choice Award winner is Ford Otosan for an automotive fan shroud that is produced with 50% recycled material and reduces the CO2 produced in the manufacturing process.
The Automotive Fan Shroud application by Ford Otosan contains 50% recycled PP, sourced from office equipment, and is the first recycled fan shroud application in the Turkish automotive industry. Commonly, fan shrouds are made from a compound consisting of 70% virgin PP and 30% glass fibers. In this recycled fan shroud, however, Ford Otosan uses 50% recycled PP, 20% virgin PP, and 30% glass fibers. With this substitution, 2.2kg of CO2 are saved for each part. This part will be used for more than 6,000 vehicles each year.
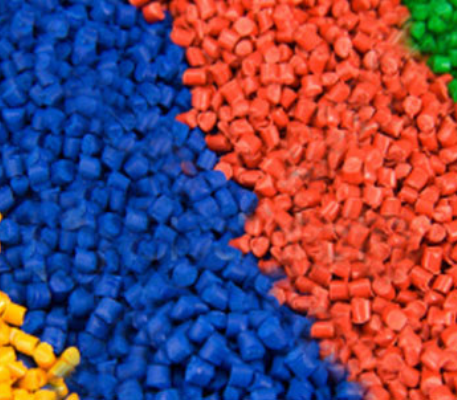
The Leadership Award, the award for the company with the best overall score across the three categories, goes to Chevron Phillips Chemical for converting difficult-to-recycle plastic waste into top-quality raw materials.
Chevron Phillips Chemical (CPChem) is the first petrochemical producer to publicly announce the successful commercial-scale production of circular polyethylene (PE) in the United States from recycled, mixed-waste plastic. This product, branded as Marlex® Anew™ Circular PE, is produced through advanced recycling technologies. It is certified recycled PE by the ISCC Plus™ approach via their rigorous mass-balance certification methodology. CPChem has announced plans to produce and sell 1 billion pounds of Circular PE by 2030.